Compression Molded Urethane Parts – Molded Parts!
Compression molded urethane parts is a high-volume, high-pressure method suitable for molding custom cast urethane parts. Urethane parts are stronger than rubber and plastic for the most demanding applications. The advantage of compression molding urethane parts is its ability to mold large, fairly intricate parts. Also, it is one of the lowest cost molding methods compared with other methods such as transfer molding and injection molding.
Compression molded urethane parts are also suitable for ultra-large basic shape production in sizes beyond the capacity of extrusion techniques. Production compression molds can hold very tight tolerances for a product that often times does not require any secondary operation. Urethane is an ideal choice for heavy loads and long service life. Most common compression molded urethane parts for Plan Tech are sprockets that drive a metal track for farm equipment. Plan Tech tested injected urethane sprockets against our hot cast compression molded urethane sprockets and found it to be over 70% stronger and resistance to tearing. Being able to cast this sprocket to size using compression molding allows us to produce thousands of high-performance sprockets. Urethane is available in any hardness or color. Special additives can also be added to increase abrasion resistance and add lubricity to the compression molded urethane parts.
Tight Tolerance Compression Molded Urethane Parts
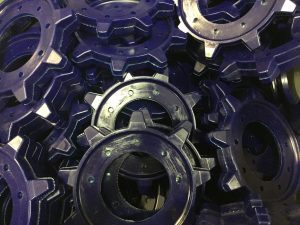
Some typical polyurethane casting options are:
Molding Urethane Parts Open cast
Open cast molding is the simplest and most common molding method for thermoset polyurethanes.
Advantages: Since pressures and temperatures in the molding process are relatively low (ambient pressure and temps below 250F), the molds are more cost effective and can be made from a variety of materials including polyurethane. Open cast molding urethane parts is good for parts with relatively open tolerances on one surface. If tolerances are tighter, a secondary finishing operation is an option.
Molding Urethane Parts Compression
The part is split on a parting line, the halves are filled and the material is allowed to gel. The mold is then closed and placed into a compression press.
Advantages: Compression molded urethane parts yield a finished part with detail on all sides. Molds can be more expensive than those used in open casting or transfer, but parts can be quite detailed and elaborate.
Compression Molded Urethane Parts
Please Contact us for further details regarding compression molded urethane parts!