Urethane Feed Rollers are used in manufacturing plants and in various pieces of industrial equipment around the world. Adding a urethane coating to the urethane feed roller will eliminate the steel contact to the product so the product is not damaged. Urethane Feed Rollers are nonmarking and will provide a smooth and quiet operation for many years. Urethane is an ideal choice when searching for a custom application due to the ease of molding or machine the urethane coating into any profile needed to match the product it will be feeding.
At Plan Tech we can strip the old worn out coating and recoat existing urethane feed roller to match OEM parts at a fraction of the cost with outstanding performance. In fact, often times our custom cast urethane feed rollers outperforms OEM products. Urethane feed rollers are commonly supplied in an 85A durometer but are available in any durometer needed for the application.
Molding Urethane Parts Open cast
Open cast molding is the simplest and most common molding method for thermoset polyurethanes. Advantages: Since pressures and temperatures in the molding process are relatively low (ambient pressure and temps below 250F), the molds are more cost effective and can be made from a variety of materials including polyurethane. Open cast molding urethane parts is good for parts with relatively open tolerances on one surface. If tolerances are tighter, a secondary finishing operation is an option.
Molding Urethane Parts Transfer and Liquid Injection
In transfer or liquid injection, pressure is used to force the liquid polyurethane out of a reservoir and into the mold. Materials are generally injected at the bottom of the part and vented at the top for the prevention of air entrapment. Advantages: Makes use of fairly low-cost molds and can achieve thin cross-sections. Parts will have a sprue and an open surface for venting air which will require a finishing operation.
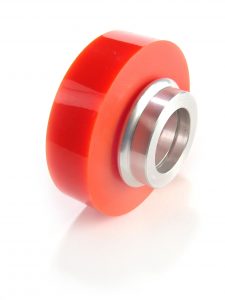
Please Contact us for further details regarding custom cast urethane feed rollers!