Urethane hole forming pins are manufactured by Plan Tech from high-quality polyurethane materials from globally recognized chemical companies. Urethane hole forming pins enable tight tolerance and controlled positioning of a workpiece. Our urethane hole forming pins offer enhanced wear properties, long service life, high abrasion and chemical resistance and a remarkable stability in environments with harsh conditions.
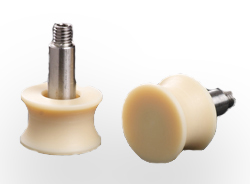
Our urethane hole forming pins are available in different coatings hence they are capable of withstanding various degrees of corrosiveness. Our team of engineers who are among the best in the industry has the technical know-how to coat our urethane hole forming pins in ways that guarantee durability. Our specialty in producing urethane hole forming pins is second to none in the industry and we have been one of the major suppliers of the product over the past 30 years. We boast one of the most fully equipped in-house machine shops in the sector just as our engineering team is renowned for their world-class capabilities. No matter the profile you need or what your requirements for urethane hole forming pins are, you can depend on us to meet your demands or specification. We always utilize speed and precision for the manufacture of all our products to ensure top-notch quality and fast turnaround.
Two common molding techniques that we utilize are:
Molding Urethane Parts Open cast
Open cast molding is the simplest and most common molding method for thermoset polyurethanes.
Advantages: Since pressures and temperatures in the molding process are relatively low (ambient pressure and temps below 250F), the molds are more cost effective and can be made from a variety of materials including polyurethane. Open cast molding urethane parts is good for parts with relatively open tolerances on one surface. If tolerances are tighter, a secondary finishing operation is an option.
Molding Urethane Parts Compression
The part is split on a parting line, the halves are filled and the material is allowed to gel. The mold is then closed and placed into a compression press.
Advantages: Compression molding yields a finished part with detail on all sides. Molds can be more expensive than those used in open casting or transfer, but parts can be quite detailed and elaborate.
Please Contact us for further details regarding urethane hole forming pins!