Urethane roller belts are produced in a variety of ways at Plan Tech which allows us to mold custom urethane roller belts in high volume. Plan Tech custom cast hundreds of thousands of urethane roller belts each year for all kinds of applications.
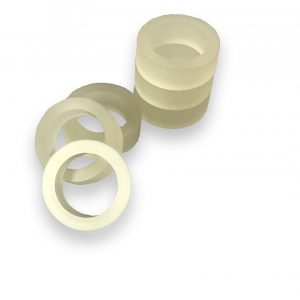
Our most popular application are replaceable urethane roller belts for a paper manufacturer. Our high-performance urethane material outlasts the original rubber belts 3:1 and is rated for just about any environment. Urethane is chemical resistant and Plan Tech has special formulas for FDA applications and high abuse applications. Most urethane roller belts consist of a simple OD ID configuration and are easily machined at Plan Tech with the use of custom build grinding and indexing equipment. Often times Plan Tech will over-mold a tube and fully machine each polyurethane drive band to ensure perfect fitment every time. Special profiles may also be molded or machined. Plan Tech blends all of our polyurethane material in our mixing department allowing us to modify our material to suit any special application. Plan Tech can also reverse engineer existing OEM urethane roller belts for a replacement that meets and often times excesses the physical properties of the original equipment.
There are several types of Molding Urethane techniques:
Molding Urethane Parts Open cast
Open cast molding is the simplest and most common molding method for thermoset polyurethanes.
Advantages: Since pressures and temperatures in the molding process are relatively low (ambient pressure and temps below 250F), the molds are more cost-effective and can be made from a variety of materials including polyurethane. Open cast molding urethane parts is good for parts with relatively open tolerances on one surface. If tolerances are tighter, a secondary finishing operation is an option.
Molding Urethane Parts Transfer and Liquid Injection
In transfer or liquid injection, pressure is used to force the liquid polyurethane out of a reservoir and into the mold. Materials are generally injected at the bottom of the part and vented at the top for the prevention of air entrapment.
Advantages: Makes use of fairly low-cost molds and can achieve thin cross-sections. Parts will have a sprue and an open surface for venting air which will require a finishing operation.
Please Contact us for further details regarding molding urethane roller belts!